Homemade Hydraulic Ram Pump
Low cost, low flow, no welding required
Page created: 20th January 2007
If you have a water supply (spring, brook or river) below the point where you need the water, and the source is higher than the lowest part of the property, then a hydraulic ram pump may be the solution. Hydraulic ram pumps are powered by a portion of the water running through it. If the cost of a commercial pump puts you off, or the water volume is too little to operate the pump, you can make one to suit your conditions at very little cost.
There are two excellent books published by Intermediate Technology on making your own ram pump. One is "Hydraulic Ram Pumps: A Guide to Ram Pump Water Supply Systems" by T.D. Jeffrey, T.H. Thomas, A.V. Smith, and P.B. Glover. The other is "A Manual on the Hydraulic Ram for Pumping Water" by S. B. Watt. I would recommend you get both; they do complement each other. They also explain how to design and build the whole system. The pumps featured in the books do require welding and threading equipment, and the smallest pump has a 2" diameter body which requires a fair amount of water to operate. However, the principle also works on a smaller scale, and I have made a pump from standard brass 28 mm compression fittings, with 28mm, 22 mm and 15 mm pipe (all readily available) and with soldering equipment. It is not scientifically worked out, but it works and is about as efficient as a commercial pump, and it takes the elbow grease out of pumping by hand or the expense and complications of an electric pump.
I don't know what the maximum lift would be with a pump this size, but in a test with my own it pumped water approximately 15 - 20 feet up with a drive head of about 5 - 6 feet. Even in such a small pump the pressure is enormous, and I believe it could pump water much higher. This pump also works on relatively small volumes of water. Even the smallest commercial pump requires large volumes of water to power it, making a ram pump unsuitable for many situations, where this smaller pump would still be able to operate. I have even operated the pump on about 25 gallons a day during a dry summer by running it intermittently from a holding tank. However, the pump only delivers about one 10th of the volume, wasting the rest, so I only ended up with about two gallons out of that tank. It also required manually opening and closing the stop cock or some complicated automated system. Self-siphoning may be a possibility I have not yet tested, but the tight pipe bends may hinder the flow too much.
I built this pump nearly 12 years ago, and did not take pictures during the build. Due to limited material choice, some parts have corroded, and some of the information is based on memory, so the instructions are a little incomplete, but hopefully there is enough information to build your own. A lot of the measurements for this pump were indeed rule of thumb - "that looks about right", and it worked. Of course, your thumb may differ in size from mine, but you get the idea.....
Click thumbnails to enlarge, click popup to close
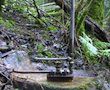
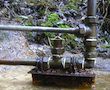
For large annotated pictures go to my Flickr page
How the Hydraulic Ram Pump Works
Typical situation where a ram pump may be used (click on image to enlarge)
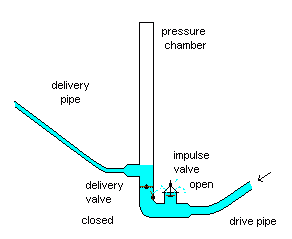
Momentum building up
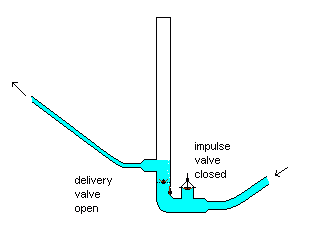
Shock wave pushes water into delivery pipe as impulse valve shuts
Water enters the ram from the thick drive pipe and runs out of the impulse valve, which is held open by a spring (or weight in larger pumps). As the momentum increases, the pressure of the water will drag the impulse valve shut. This creates a shock wave inside the ram body, pushing water past the delivery valve (a non-return valve). As the pressure subsides the impulse valve opens and the cycle begins again. This takes place more than 100 times a minute, depending on the head pressure and tuning of the impulse valve, and each pulse pushes up a small quantity of water through the thinner delivery pipe. The air chamber cushions the flow. The tiny snifter valve below the chamber allows a small quantity of air into the air chamber with every pulse to replace air lost into the deliver pipe. A small squirt of water will come out on the recoil.
Building the pump
Materials
- approx. 1 meter of 28 mm copper pipe for body and pressure chamber
- 22 mm copper pipe for supply pipe
- 15 mm copper pipe for delivery pipe
- connectors as needed
- two 28 mm compression 'T's
- one 28 mm compression elbow
- one 28 mm solder blank end - optional
- one 15 mm ball valve
- one 28 mm to 15 mm reducer - solder type
- one 28 mm to 22 mm reducer - solder type
- flat piece copper for valves (pipe cut open and hammered flat on metal surface)
- small bore pipe to form guide for impulse valve
- inner tube for delivery and snifter valves and mounting shock absorbers
- rubber and copper disk (psst! don't tell Her Madge - a coin) for impulse valve
- tiny nut and bolt cut from earth connector of light switch for snifter valve flap
- two nuts and bolts for the impulse and the delivery valve - brass or s/s
- a steel spring removed from a cabinet ball and spring closure (brass would be better if found) for the impulse valve
- 1/2 tea strainer (wire globe type) clipped to tank outlet
- approx 1 ft of 22 mm i/d reinforced automotive rubber pipe as shock absorbing section in supply pipe
- two hose clamps for above
- one 20 gallon tank as buffer and filter at spring
- one 22 mm tank connector
- two exhaust pipe brackets to hold pump body to base
- section of steel I-beam for base, or similar
- concrete to hold pump base
- solder, flux
Note on fittings - these compression fittings are typical for the UK, and are somewhat different from those available in other countries. Your fitting may look different, but should still work. It is important to use threaded fittings, as the rubber gaskets in the pump body would be damaged when assembling a pump made with solder fittings. Threaded fittings also allow access to the inside of the pump in case of debris entering it, or to replace worn gaskets. Although I used joint tape, it is probably not necessary, as a slight seepage is of no consequence in the pump setting, and the amount of water lost miniscule.
You may be able to obtain the short length of pipe and fittings for the body from a plumber doing a remodelling job. If you buy new materials, shop around. I have bought the fittings at an agricultural iron mongers for about one third the price a builder's merchant charged! The most difficult thing to obtain is the right size brass nuts, bolts, and spring. DIY shops have very little choice - if you get the right length bolt, it may be too thin.
You may be able to scavenge them from some old electrical equipment, as did I, if only I could remember what from. Make sure it is solid brass as any plating will soon wear off. Valve gaskets can be cut from inner tube, preferably car tube, as it makes flatter gaskets. Avoid seams. The spring for the impulse valve came from a cabinet ball snap closure. It was just the right size and tension, but made of galvanised wire, which did not last long. You may be able to make one from s/s or brass wire. This is the part which needs some experimentation.
Delivery and Snifter Valve Assembly
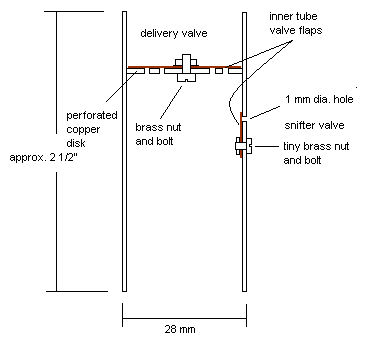
Delivery valve assembly
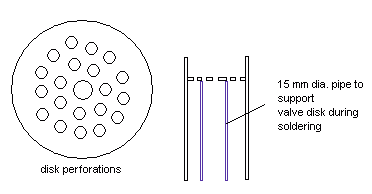
Delivery valve disk and solder support
Cut a disk of sheet copper (a piece of opened up pipe, hammered flat) to fit inside the approx. 2 1/2 inch section of 28 mm pipe. Drill one hole in the centre to take a small bolt, and holes all around to allow as much water through as possible, but not so many to weaken the disk. Leave a solid edge for the gasket to overlap enough to prevent leakage. File the holes clean with a round needle file and rub surface with abrasive paper to prevent sharp edges and to ensure the gasket makes good contact. Solder the disk into the pipe about 1/2 inch below the edge. Rest the disk on a piece of 15 mm pipe cut to the hight of the disk position. Keep it to the centre and avoid excess solder, or you will solder this pipe to the disk too.
Drill a 1 mm diameter hole about halfway down the pipe, and clean the edges. Drill another hole about 1/4 inch below, making it the size of a tiny bolt. Cut a small flap of inner tube to cover the 1 mm hole and extend beyond the bolt hole, and cut a small hole in the rubber for the bolt. Attach the rubber flap with the bolt and nut. If you can't find a tiny brass nut and bolt, you can improvise with the small grub screw and the threaded counterpart of the earth terminal of a redundant plastic electrical socket. The threaded brass block should be sawn in half to reduce drag.
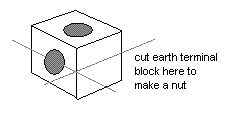
Cutting of brass terminal block to make nut for snifter valve
Cut a disk of inner tube to fit snuggly inside the pipe, but not touching the pipe, as the flap must be able to move freely. Cut a small hole in the centre and bolt it on top of the metal valve disk with a small washer between the gasket and the nut.
Impulse Valve Assembly
This one is more tricky to make, and will need some experimenting and improvising with available materials. I will describe the one I made, but there are many ways of doing it. The main principle is a rigid disk with a rubber surface (for good contact) on a guided support which allows the disk to travel in a straight line. The disk is held away from the opening with a spring or weights, which should not prevent the shock wave from slamming the valve shut. The valve disk should be smaller than the inside diameter of the valve body to allow water to pass around it to exit from the outlet holes which need to be big enough to allow the water to pass through with as little resistance as possible to build up momentum. In practice this is a compromise between the disk size and the outlet holes. If the outlet holes are too big, then the disk would have to be correspondingly big to cover the holes in the shut position, thereby allowing little water to pass around the disk when open. The area of the holes should be about equal to the area of the space around the disk, taking into account a small area where the disk overlaps the outlet plate to ensure a tight seal.
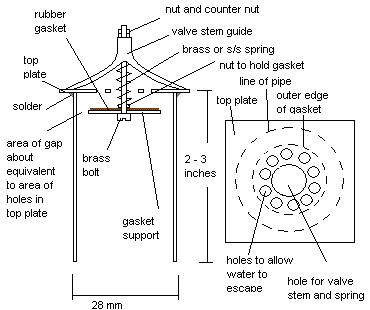
Impulse valve assembly and top plate
Cut a section of 28 mm pipe to about 2 - 3 inch length. Make a flat piece of copper to cover the top which overlaps the edge to give a sufficient mounting surface for the valve stem guide. Shape is not important, though square is probably easier, unless you already happen to have a suitable round disk.
Drill a large enough hole in the centre to allow the spring to pass through without catching the edge, and drill more smaller holes around this big one, using the above thumb formula. I am not sure why I did not make a larger hole instead. The reason may have been drill size. I suppose, one large hole should work as well, as long as it is a smaller than the valve disk to allow the sealing overlap. Make sure the holes and surface are smooth. Solder a frame to the top of the plate to hold a piece of tube just big enough to allow the bolt to pass through and guide it in a straight line. I happen to have had some thin copper tube scavenged from a gas installation of an old caravan.
There were two diameters, one fitted snuggly inside the other. The inner was just big enough for the bolt (taking into account that the thread will be filed off the bolt inside the guide tube), but did not have enough substance to split it into four extended legs to support it above the plate, but the larger tube served that purpose. I then soldered the legs to the top plate. The guide tube should also be small enough for the spring to but against it, and not slip inside. The height should allow for the spring to be in the relaxed position with the valve disk about the same distance below the top plate in the open position as the space around the disk. It should also allow room for compression of the spring when the valve shuts, i.e. the spring should also be long enough to allow this compression without the bunched up wires crowding the small space between the guide and the top of the plate, which would happen with a short and tightly coiled spring.
To assemble the valve drop a copper or brass disk onto the bolt head followed by a rubber disk, a washer and a nut to secure the disks. Measure the length of the spring and the guide tube and file the thread off the bolt for this length to prevent snagging, and leave thread on the last section for the nut and counter nut. Drop the spring onto the bolt and feed the bolt from inside the valve body through the centre hole and the guide tube and secure the bolt in place with the nut and counter nut.
Assembling and Installing the Pump
Assembling is very easy, just follow the diagram. One point to watch out for is the location of the snifter valve. When inserting the deliver valve assembly between the elbow and 'T' make sure the snifter valve is on the opposite side of the delivery pipe exit to prevent the air being lost up the delivery pipe. The top of the pressure chamber can be capped with a blank end or simply hammered flat, bent over like a toothpaste tube, and sealed with solder run into the joint.
It is critical that there is enough water to power the pump, as any reduced flow would simply trickle out of the open impulse valve without causing the shock wave to slam it shut. The pipes need to be filled and no air should enter the pipe. It is also important that no debris enters the pump as it can easily jam the valve open. Some kind of intake tank is advisable, and a filter at the tank exit. I used a 25 gallon plastic tank and clipped one half of a s/s fine wire mesh tea strainer (the wire globe type with sprung handle) over the tank connector nut - just happened to be perfect fit.
The water also came from a covered spring with very little debris entering it. The drive pipe needs to be as straight as possible, with any bends kept very gradual. Stop cocks must not hinder the flow, therefore a ball valve would be best suited. The jolt of the valve slamming shut creates a fair amount of pressure in the pipe, and it needs to have some shock absorbing section of strong reinforced rubber hose in the upper section. The pump body must be fixed to a base rigidly, but with some cushioning.
I clamped the pump to a section of 'I' beam which is embedded in concrete, and used exhaust pipe clamps, cushioned with some inner tube wrapped around the pump body. There is a stop cock on both pipes entering and leaving the pump. For the longer delivery pipe Medium Density Polyethylene is best suited for longer sections, and can easily be joined at or near the stop cock with a copper to MDPE adapter.
Update
I had an email from Helen, who drew my attention to a swing check valve, which has a hinged flap and may be used for the impulse valve. She also suggested that the delivery valve could be a spring check valve. Both should be readily available at plumber's merchants. It is worth an experiment, and would further simplify the production. Helen will come back with any results, if she makes a pump with those parts.